PRODUCTION
Production under control: Guaranteed results
At Aldicast, we monitor every parameter of our production processes in real time. All manufacturing data is recorded by batch, ensuring traceability, repeatability, and quality.
We commit to a production model based on Industry 4.0 principles, integrating automation, predictive analytics, and flexibility from design to final product.
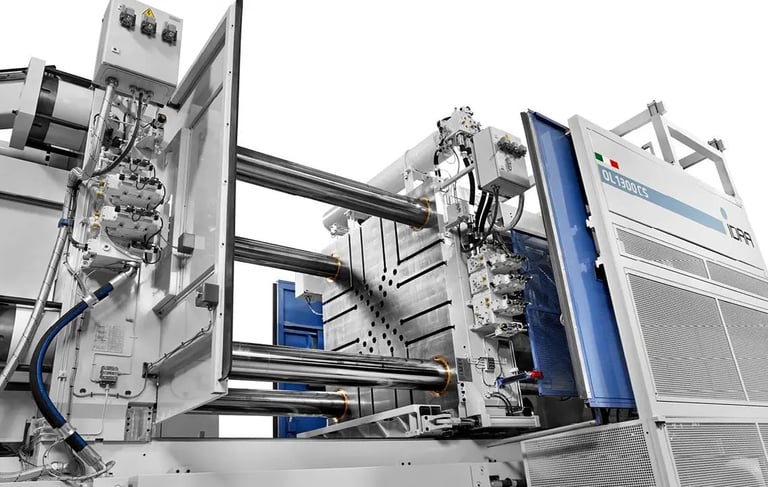
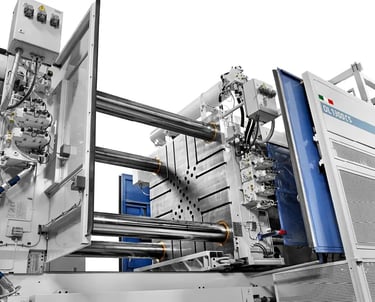
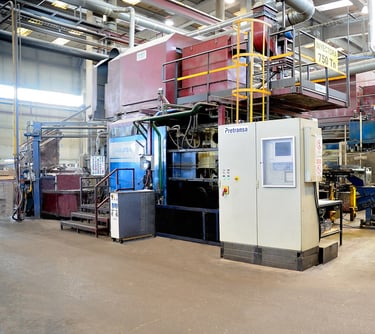
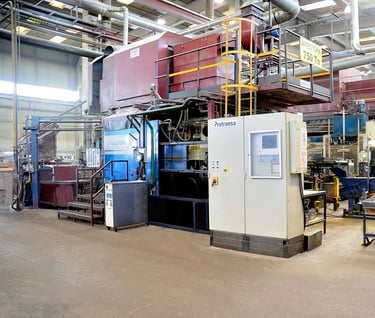
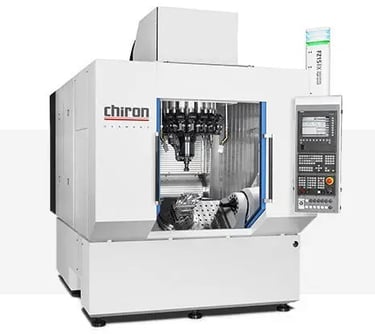
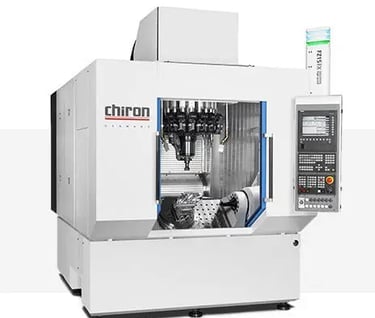
CNC MACHINING CENTERS
ROBOTIZED AND AUTOMATED, WITH INTEGRATED QUALITY CONTROLS.
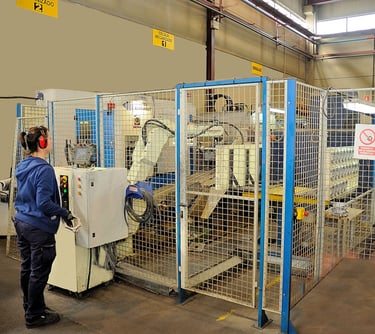
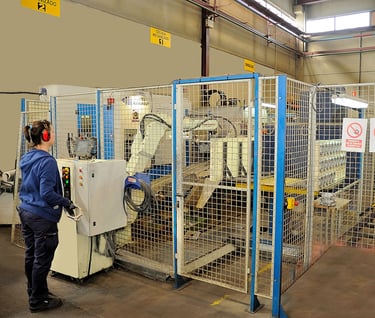
TRANSFER MACHINES
AUTOMATED, ROBOTIZED, AND SPECIFICALLY DESIGNED FOR EACH PROJECT.
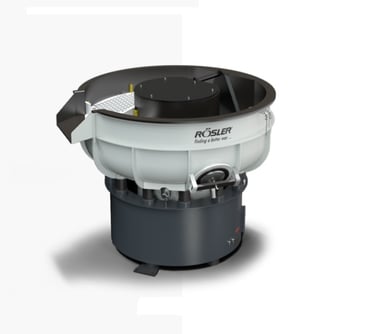
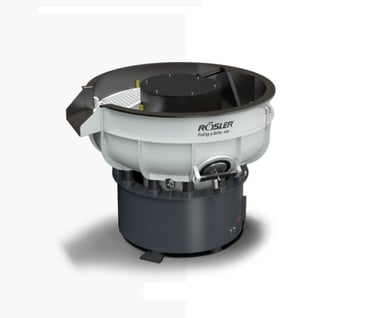
Production means: Technology at the service of the process
SURFACE FINISHES
SHOT BLASTING AND VIBRATING OF PARTS.
INJECTION CELLS
100% AUTOMATED CELLS FROM 700 TO 1,300 TONS, EACH EQUIPPED WITH INDIVIDUAL MELTING FURNACE, DIE, AND SHOT BLASTING MACHINE. TOTAL PROCESS CONTROL.
Aldicast works with multiple aluminum alloys, adapting to customer needs and the type of part.
Our cells with individual melting furnaces allow us to work with different alloys simultaneously, guaranteeing flexibility and competitive delivery times.
VERSATILITY IN ALLOYS
Mold and Tooling Development
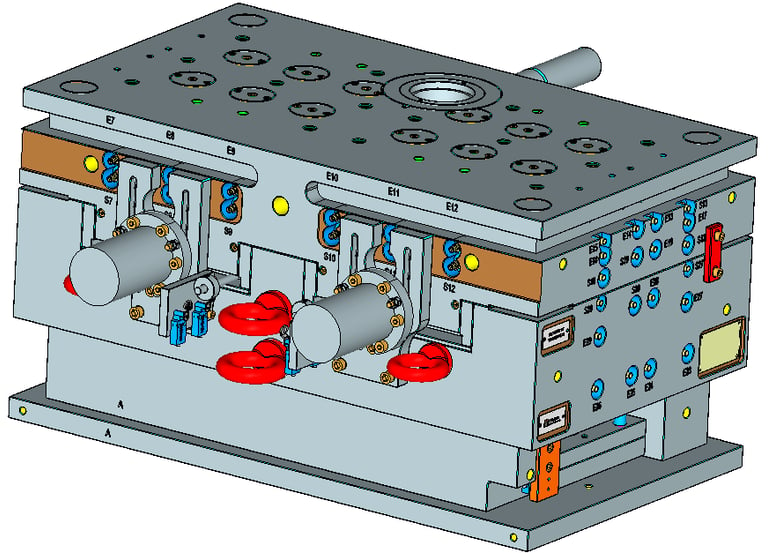
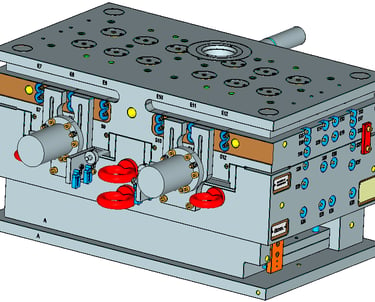
Aldicast has a strategic partner for the design, manufacturing, and maintenance of top-level tooling. We develop high-quality molds, dies, control fixtures, and machining tools.
Our engineering department manages all stages of tooling production to ensure compliance with productivity, quality, and durability requirements.
Finishes and Treatments
Our main activity is high-pressure aluminum die casting followed by machining. We offer a wide range of treatments to adapt each part to its final application:
Shot blasting
Vibratory finishing
Heat treatments
Electrolytic treatments
Impregnation
Pickling
Liquid or powder painting
Chrome plating
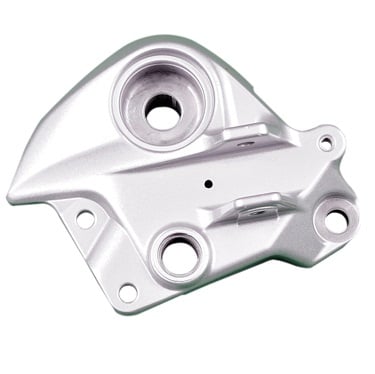
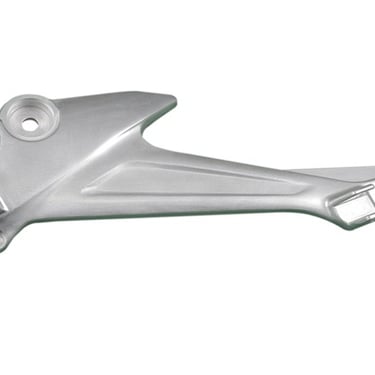

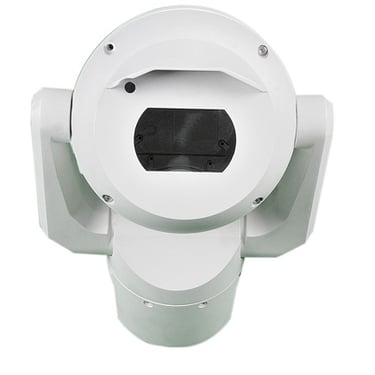
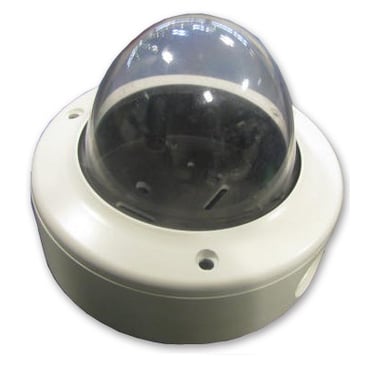